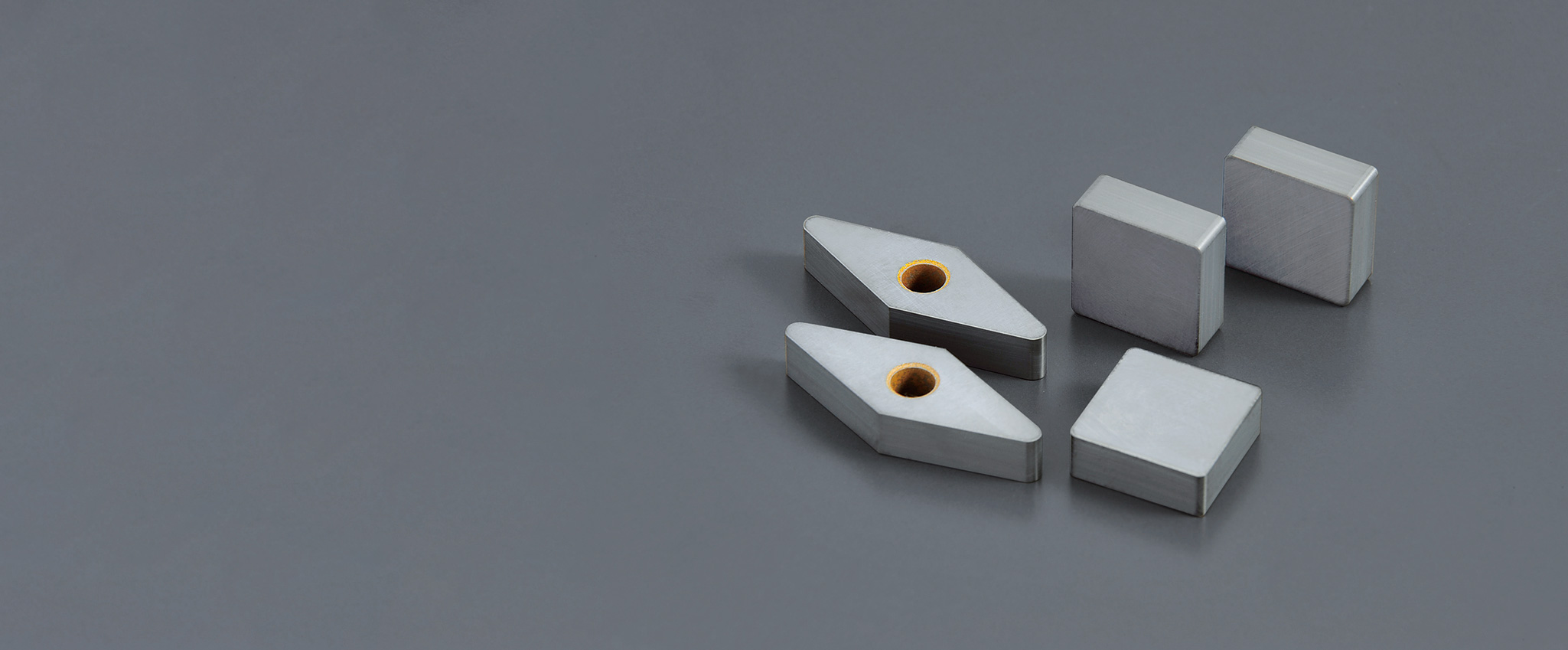
Machine gray cast iron at Speeds ~ 1200 M/min
- Outstanding boundary wear resistance
- Outstanding thermal shock resistance
Features:
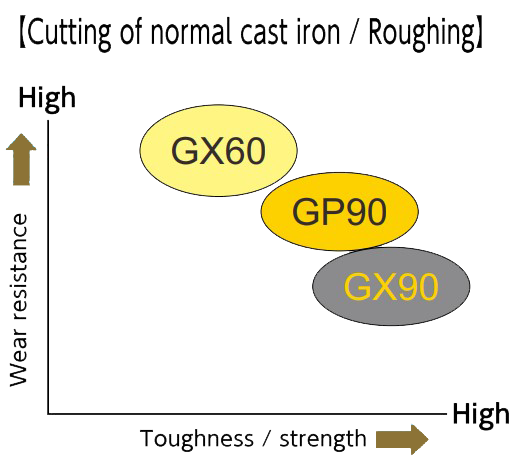
Tooling application
- Gray cast iron with scale
- Rough Turning / Milling
Why is silicon nitride ceramic resistant to chipping?
The main component is silicon nitride(Si3N4), which differs from alumina-based materials in that its particles are needle-like.
The intertwining of the needle-like particles greatly suppresses the progression of cracks caused by impact during cutting and prevents chipping.
Cutting conditions
Grade | Material | Operation type | Machining | Cutting speed (m/min) | Feed (mm/t – mm/rev) | DOC(mm) | Coolant |
GX60 | Gray cast iron | Turning | Roughing with scale, Rough to semi-finish machining | 500 -1100 | 0.3 – 0.6 | -5.0mm | DRY / WET |
Milling | 500 -1250 | 0.07 – 0.25 |
Grade | Material | Operation type | Machining | Cutting speed (m/min) | Feed (mm/t – mm/rev) | DOC(mm) | Coolant |
GX60 | Gray cast iron | Turning | Roughing with scale | 500 -1100 | 0.3 – 0.6 | -5.0mm | DRY / WET |
Milling | Rough to semi-finish machining | 500 -1250 | 0.07 – 0.25 |
Gray cast iron roughing application
Brake disc
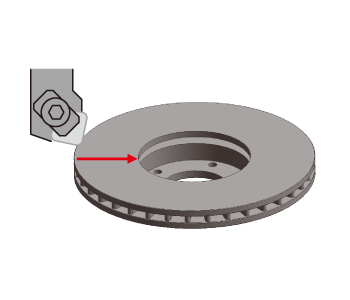
Material | FC150 with scale |
Cutting speed | 1100 m/min |
Feed | 0.5 mm/rev |
DOC | 2.0 〜 3.0 mm |
Coolant | WET |
GX60 | 75 pcs/Corner |
Competitor’s Tool | 50 pcs / corner |
Milling Application
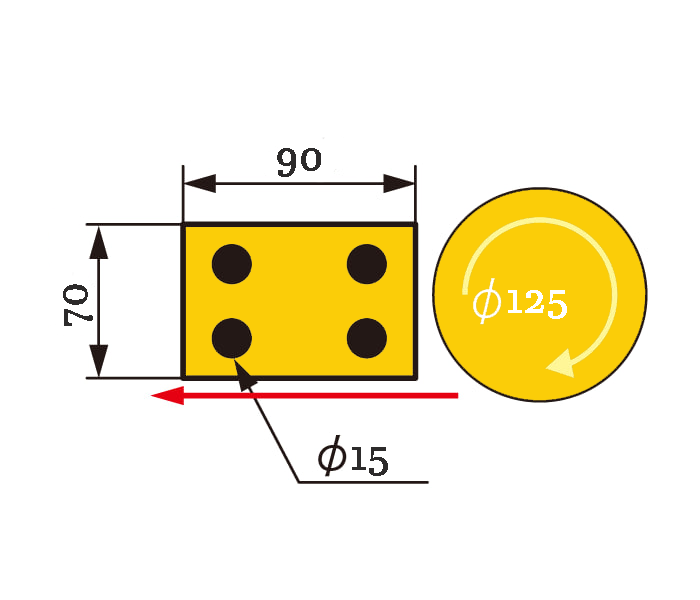
Material | FC270 |
Cutting speed | 800 m/min (GX60) 145 m/min (Competitor’s carbide) |
Feed | 0.06mm/t (GX60) 0.2mm/t (Competitor’s carbide) |
DOC | 1.5mm |
Coolant | DRY |
GX60 | 360 pcs / corner |
Competitor’s carbide inserts | 260 pcs / corner |
High-speed milling with ceramic significantly reduced cycle time compared to the current carbide inserts. (Single pass process went from 40 min. down to 15min.)
GX60 achieved 1.4 times more tool life.
Tooling costs are reduced by utilizing negative inserts, increasing the number of corners.